Other Types of Oxidizers:
Manufacturers of Oxidizer Equipment:
Regenerative Thermal Oxidizer
What is a regenerative thermal oxidizer?
A Regenerative Thermal Oxidizer (RTO) is an industrial-grade air pollution control device that use high temperatures to combust and decompose volatile organic compounds (VOCs) into CO2 and water vapor.
Also known as an RTO, a regenerative thermal oxidizer heats the VOC-laden process exhaust gas to temperatures in the range of 1400-1500°F, triggering thermal decomposition, also known as a combustion reaction.
Regenerative Thermal Oxidizers (RTOs) are available in many different shapes and sizes. The two main designs are the 2-tower and 3-tower RTO (may also be called a 2-can or 3-can RTOs). The 2-tower design will suit most cases, providing up to 98% destruction & removal efficiency (DRE), while the 3-tower design will be used when the highest destruction efficiency (99%+) is required (in cases of odor complaints, for example).
Regenerative Thermal Oxidizer (RTO) equipment is used to destroy VOCs and other organic hazardous air pollutants. They are not good for treating particulates, inorganic gases, heavy metals, acids, nor other corrosive gases. If these other contaminants are present, a Regenerative Thermal Oxidizer (RTO) could be used in combination with a dust collector or wet scrubber, depending on the situation.
Regenerative Thermal Oxidizer effectiveness on:
*Note: an RTO may not be effective at removing inorganic odor compounds.
How Much Should It Cost? Find a Supplier, Get a Quote.
Main components of an RTO
Ductwork and Fan/Blower
Regenerative Thermal Oxidizers (RTOs) will use either a forced draft or induced draft fan system, depending on the process air temperature. Installing the fan on the coolest side offers the best performance.
Combustion Chamber and Burner
At the top of the towers sits the combustion chamber which connects all the towers together in the Regenerative Thermal Oxidizer (RTO) system. Air passes up through one tower then passes horizontally through the upper combustion chamber and across the burner then finally passes down through another tower.
Ceramic media towers
Regenerative Thermal Oxidizers (RTOs) achieve 95% thermal efficiency by absorbing and storing the waste heat from combustion in large towers of ceramic media. By periodically switching the airflow direction, the waste heat stored in the media may be released to heat incoming air.
Switching Air Valves
The Regenerative Thermal Oxidizer (RTO) will periodically cycle each tower between (Cycle 1) admitting dirty process air and releasing heat from ceramic media, (Cycle 2) purging and cleaning, or (Cycle 3) exhausting and absorbing heat from post-combustion air into the ceramic media.
Heat Exchanger and Stack
After passing through the combustion chamber of the regenerative thermal oxidizer, the air can be extracted and used to heat other process liquids or gases via a heat exchanger. Otherwise the clean air passes down through a ceramic bed, releasing its heat, then is exhaust via a stack.
Operation: How does a Regenerative Thermal Oxidizer (RTO) work?
The left tower's inlet air valve is in the open position, allowing VOC-laden dirty air to be pushed into the first chamber by the fan at left. The first tower (Chamber 1) is hot from the last cycle and is now releasing heat to warm the incoming dirty air as it moves upwards through the first chamber.
The pre-heated air now passes into the center combustion chamber, reaching temperatures of 1500°F, and thermally combusting, decomposing into CO2 and water vapor. Some new technologies use a burner-less operation that utilizes natural gas injection, once at steady-state.
The right tower's exhaust air valve is in the open position. Clean, hot air now travels down the right tower (Chamber 2) and out the stack at left. The ceramic media in this chamber is warming up by absorbing heat from the outgoing clean air. It will be hot by the end of this cycle.
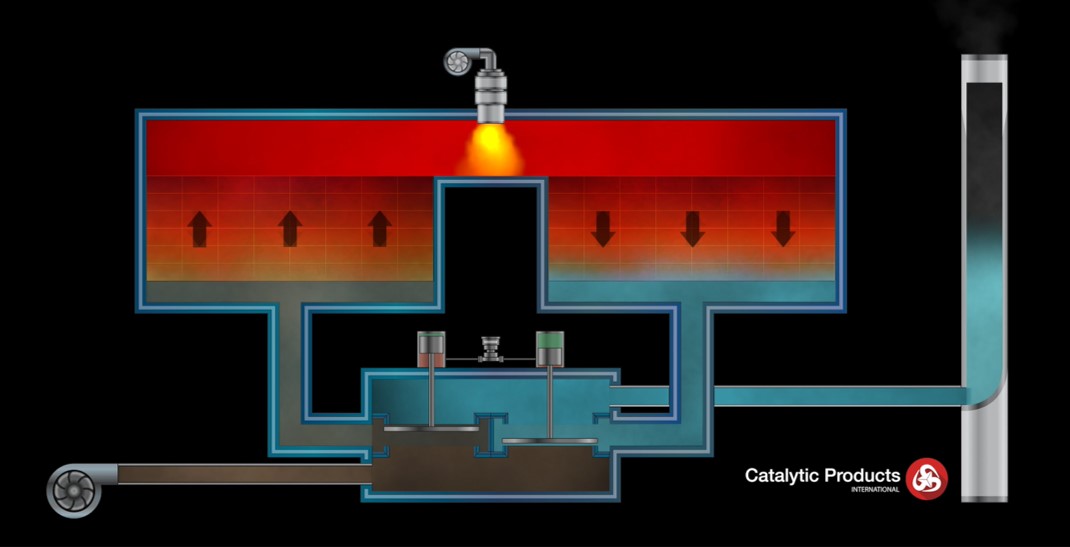
A flow schematic for a 2-tower regenerative thermal oxidizer (RTO).
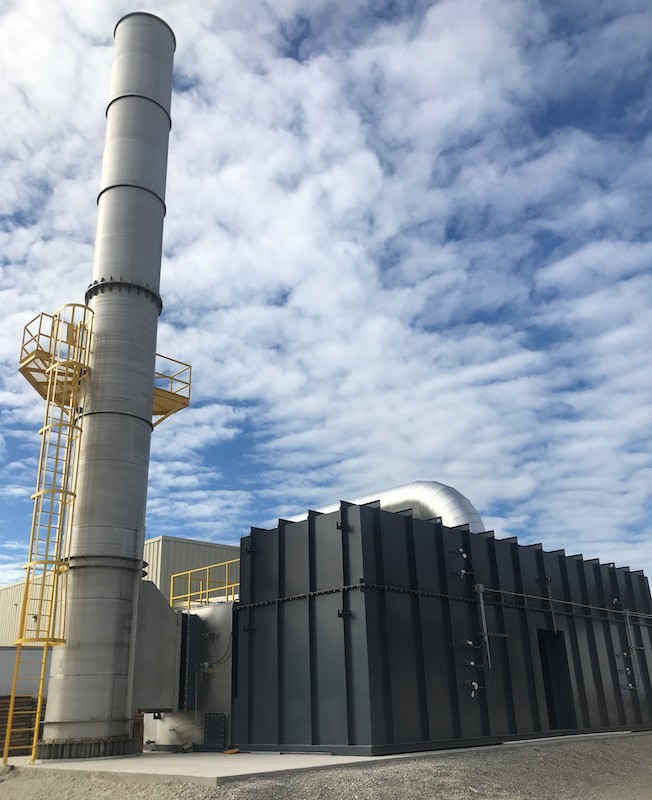
A two-tower regenerative thermal oxidizer (RTO) from Catalytic Products (CPI).
Used for industrial applications with volatile organic compounds (VOCs).
RTO Design Considerations
Air Volume Flowrate (CFM)
The volume of process air to be treated is a key consideration. A single Regenerative Thermal Oxidizer (RTO) system can be designed to handle any amount from 1,000 CFM to over 50,000 CFM. Multiple Regenerative Thermal Oxidizers (RTOs) can be combined to treat any volume of air.
Destruction or Removal Efficiency (DRE)
Factors that impact DRE:
- Temperature
- Residence time
- Purge cycle
- Two-cycle no purge (2-tower RTO)
- Three-cycle with purge (3-tower)
Materials of Construction
Material options include:
- Stainless steel
- Carbon steel, painted
- Aluminized steel
- Galvanized steel
- Insulation and cladding
- Dampers
Equipment Configuration & Layout
Key questions include:
- Are multiple control devices needed?
- Due to high air volume -> 2 RTOs in parallel
- Due to multiple contaminants -> equipment in series
- Is a scrubber required? (Scrubber + RTO combo)
- Fan location: induced draft or forced draft?
- Type of valves: compressed air (pneumatic), hydraulic, poppet, or rotary
- Inlet ductwork, outlet ductwork and exhaust stack
- Test ports & access platforms
Do you need to find RTO suppliers?
Use our free Find Suppliers tool.
Industries, Applications, & Case Studies
Regenerative Thermal Oxidizers are used in a wide variety of industries and applications, including:
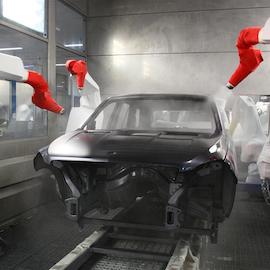
Automotive
-
Regenerative Thermal Oxidizers (RTOs) are used in automotive, marine, and other vehicle manufacturing for treating VOCs from paint booths, controlling HAPs from paint curing ovens, engine test and quality control, tire manufacturing, and component painting. The high volume, low concentration conditions are ideal for a regenerative thermal oxidizer.
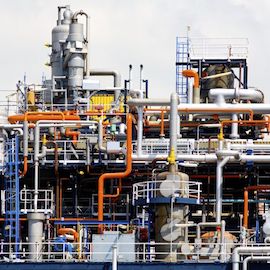
Chemical Processing
-
Manufacturing or processing chemicals generates exhaust air contaminated with toxic gases and VOCs. These vapors need to be captured and treated prior to release to atmosphere. An RTO is the most robust solution for these applications: tank vents, separators, acid gases, chemical production, and ceramic kilns.
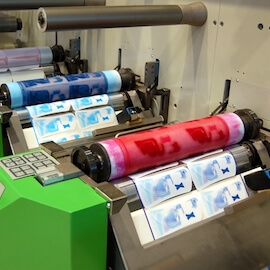
Printing
-
Printing operations require VOC abatement, use of Permanent Total Enclosures (PTEs) for fugitive emissions capture, odor elimination, and toxic fumes destruction. An RTO is an effective control device for Flexographic, Web Offset, Rotogravure, and Converting processes to treat water or solvent-based inks and exhausts from dryers/ovens.

Ethanol & Biodiesel
-
The production of ethanol and biodiesel fuels from dried, distilled grains like corn or cellulose plants creates airborne VOCs, NOx, odors, particulate matter (PM), aerosols, and other Hazardous Air Pollutants (HAPs). A Regenerative Thermal Oxidizer (RTO) is a reliable solution for your kiln and dryer emissions.
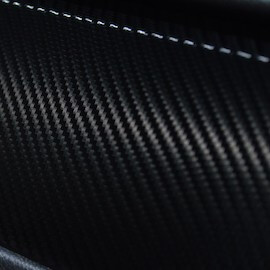
Composites & FRP
-
A Regenerative Thermal Oxidizer (RTO) is an appropriate solution for abating the air pollutants from Carbon Fiber, FRP, Fiberglass, and other composite manufacturing. Composite resins contain styrene that needs to be thermally treated before emitting to atmosphere. Other pollutants from ovens and furnaces include Hydrogen Cyanide, Ammonia (NH3), and Nitrous Oxide (NOX).
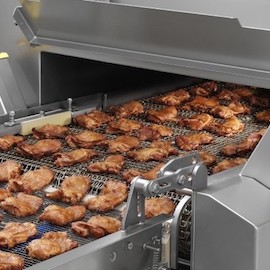
Food, Meat, Bakery
-
Food production creates odors which often need to be controlled prior to emission. A three-tower RTO is the ideal solution for to controls odors in large-volume exhausts. The 3-chamber regenerative thermal oxidizer offers 99+% control. Smaller exhaust volumes can use a recuperative thermal oxidizer with heat exchanger.
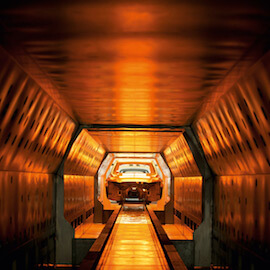
Industrial Ovens
-
Industrial ovens for curing parts, paints, and coatings generates air pollution and contaminants that need to be captured and controlled. The oven will flash off VOCs and other HAPs that need to be destroyed by an RTO or other thermal treatment device.
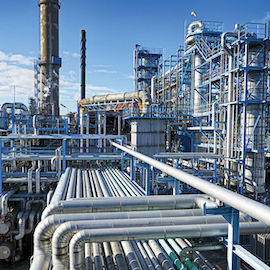
Natural Gas Processing
-
RTOs are a popular air pollution control device for off-gas treatment from Natural Gas processing, including VOCs and HAPs from amine tail-gas treatment systems, sulfur recovery units, nitrogen rejection units (NRU), glycol regenerators, liquefied natural gas (LNG) processes, and storage tank venting.
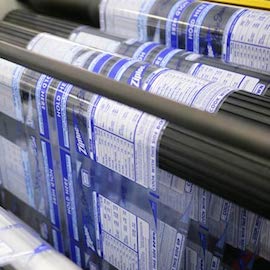
Packaging & Labeling
-
Applying coatings, graphics, and adhesive labels to flexible packaging or metal containers releases VOCs that need to be captured and destroyed. A regenerative thermal oxidizer (RTO) is the most robust solution to treat both the application and drying air streams.
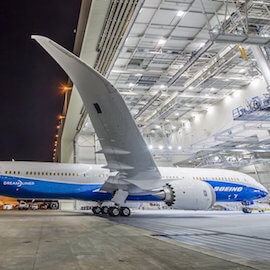
Paint Booths & Hangars
-
Paint Booths in the Automotive, Industrial, Aerospace, or vehicle OEM industries require high-volume, low-concentration VOC abatement that is well suited to Regenerative Thermal Oxidizers (RTOs). The high-flow downdraft or cross-draft paint booths often use a dry-filter and or wet scrubber system to catch the paint overspray and dried particulate prior to the final VOC destruction device.
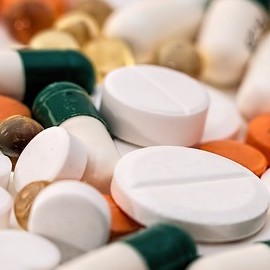
Pharmaceutical
-
Tablet coating, fluid-bed processing, and tray drying in the Pharmaceutical industry offers unique air pollution control challenges as the ethanol, isopropyl alcohol (IPA), and other VOCs often releases into concentrations in excess of 100% LEL. This poses a fire and explosion risk, so dilution air is required for plant safety. An RTO is often used as the final control device.
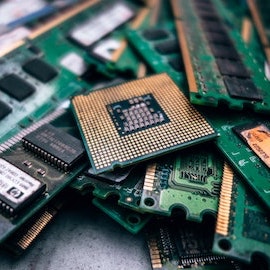
Semiconductor
-
In the semiconductor industry, RTOs are used for control of VOC emissions from chip manufacturing, LCDs, printed circuit boards (PCBs), and more. RTOs are highly robust, operating 24/7 for 50+ weeks per year with minimal downtime. They can be designed to withstand corrosive acids or other destructive solvents in the exhaust.
Recommended RTO Manufacturers
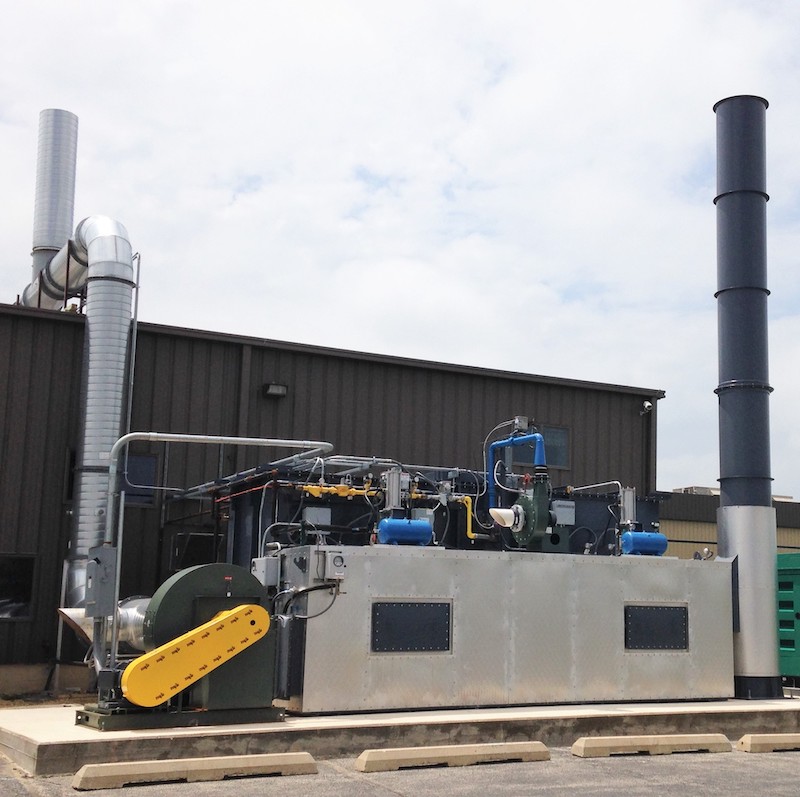
RTO: Optional Equipment
Natural Gas Injection
Natural Gas Injection, a.k.a. Supplemental Fuel Injection or Flameless Operation, is a method of RTO operation where the combustion chamber is operating without an open flame. At the inlet to the RTO tower, natural gas is injected into the incoming dirty air stream to increase the VOC concentration to ~3-5% of LEL. At this concentration, as long as the combustion chamber is operating at temperature set point (~1500°F), the VOCs will combust fully without an open flame, generating heat to maintain the set point, and the reaction will continue.
The main advantages of natural gas injection are:
- Minimizing silica (SiO2) formation
- Reducing natural gas consumption
- Lowering NOX emission levels.
Specialized Ceramic Media Bed
- Random packing
- Saddles
- Monolith
- Structured media
- SiO2-Resistant (silica-resistant) structured ceramic media
- Corrosion resistant coating
Waste Heat Recovery
For sufficiently large RTOs, the waste heat from the RTO (~200°F) may be captured and used to heat process air or liquids. For example, RTO waste heat can be used to heat drying ovens, generate hot water, heat the plant in the winter, or another 100-200°F application.