Other Types of Oxidizers:
Manufacturers of Oxidizer Equipment:
What is a thermal oxidizer?
A thermal oxidizer (also known as thermal oxidiser, fume incinerator or thermal incinerator) is a type of air pollution control equipment used in industrial processes to reduce emissions of volatile organic compounds (VOCs), odors, harmful air pollutants (HAPs), and other greenhouse gases (GHG) before releasing them into the atmosphere.
How does a thermal oxidizer work?
Using extreme high temperatures (1500°F) to trigger a combustion reaction, the VOCs & air pollutants undergo thermal oxidization, transforming the organic solvents into CO2 (carbon dioxide) and H2O (water).
Similar to an incinerator, a thermal oxidizer is an EPA-approved device to treat VOCs, odors, HAPs, contaminated gases, and aerosolized solvents.
Types of thermal oxidizers:
Direct-fired Thermal Oxidizer (DFTO)
The simplest type of thermal oxidizer, it's just a burner in a box with a fan. The direct-fired TO does not have any heat recovery system. This is the least expensive type of equipment, but has the highest energy costs.Thermal Recuperative Oxidizer (TRO)
The recuperative type features an air-to-air heat exchanger (HEX), and uses the waste heat to pre-heat the incoming air to the burner. The TRO offers 60-70% thermal efficiency. It's more expensive than the DFTO, but offers lower energy costs.Regenerative Thermal Oxidizer
(RTO) The most common type of oxidizers, the RTO uses ceramic media to capture and recycle waste heat, offering 95% thermal efficiency. The RTO is the most expensive type of thermal oxidizer, but offers the lowest energy costs.Gas Flare (Vapor Combustor)
While not technically a type of thermal oxidizer, the flare is similar to the direct-fired oxidizer but it does not require supplemental natural gas. Flares are used on very high concentration VOC gas streams (over 3-5% of LEL).Catalytic Thermal Oxidizer (CATOX)
This type uses a metal catalyst to speed along the VOC's decomposition reaction. The main advantage of catalytic thermal oxidizers is that they can operate at much lower temperatures of 800°F-900°F instead of 1400°F-1500°F.Recuperative Catalytic Oxidizer (RCO)
Similar to the catalytic oxidizer above, the RCO adds a heat exchanger for waste heat recovery. The RCO is a more expensive type of catalytic oxidizer, but it offers lower operating costs.
Thermal Oxidizer Efficiency
*A thermal oxidizer may not be effective at removing inorganic odor compounds.
*A Rotary RTO or Three-chamber RTO will be the most effective at removing odor compounds.
*Note: only direct-fired and recuperative oxidizers are effective at treating particulates.
Main components of a Thermal Oxidizer
Ductwork and Process Fan
A thermal oxidizer will typically use a forced-draft fan setup instead of an induced-draft fan system, because the process air temperature is usually cooler on the inlet side. Installing the fan on the coolest side offers the best fan performance due to increased air density at lower temperatures.
Combustion Chamber (Firing box)
The primary component of a thermal oxidizer system is the combustion chamber, or firing box, which houses the burner. Contaminated air passes through the combustion chamber, designed to provide enough time at temperature (residence time) to achieve the desired destruction efficiency (DRE).
Burner, Gas Train and Combustion Blower
The heat-generating system of the thermal oxidizer is comprised of the burner, gas train, and combustion blower. The gas train provides natural gas and the combustion blower provides ambient air with oxygen for combustion. Most burners come equipped with an ultra low NOX controller to tweak the air and fuel mixture to increase flame size and reduce peak flame temperatures, thereby reducing NOX production.
Primary Heat Exchanger
In a recuperative or regenerative oxidizer design, there is a primary heat exchanger to use the hot, clean air exiting the combustion chamber to pre-heat the incoming dirty air. In the recuperative oxidizer design, the heat exchange is via an air-to-air heat exchanger (HEX). In the regenerative oxidizer design, the heat exchange using multiple ceramic media chambers.
Secondary Heat Recovery and Stack
After passing through the primary heat exchange, the air is still quite warm (200-600°F), and can be used to heat other process liquids or gases via an optional secondary heat exchange. After passing through the heat exchanges, the clean air is exhaust to atmosphere via a stack.
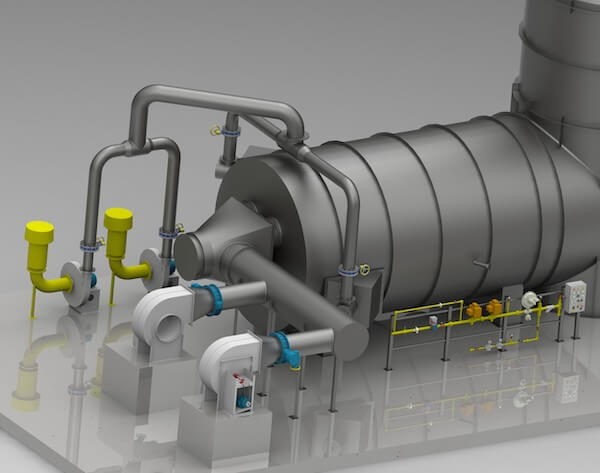
A 3-D CAD rendering of a direct-fired thermal oxidizer (DFTO).
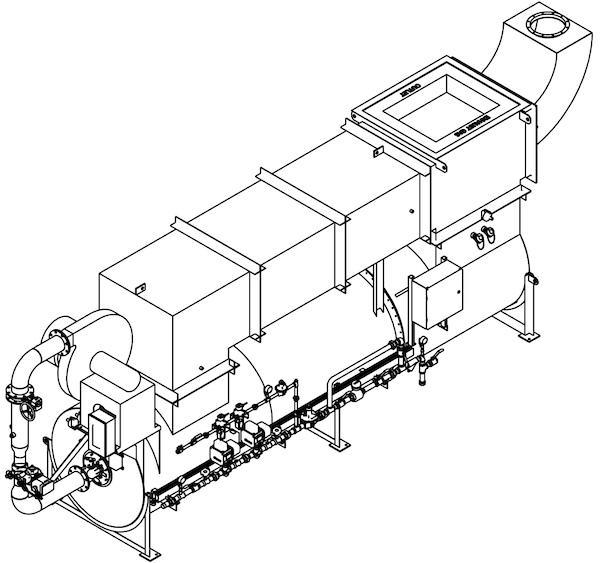
A drawing of a basic thermal recuperative oxidizer (TRO),
with primary heat exchanger mounted on top.
How Much Should It Cost? Find a Supplier, Get a Quote.
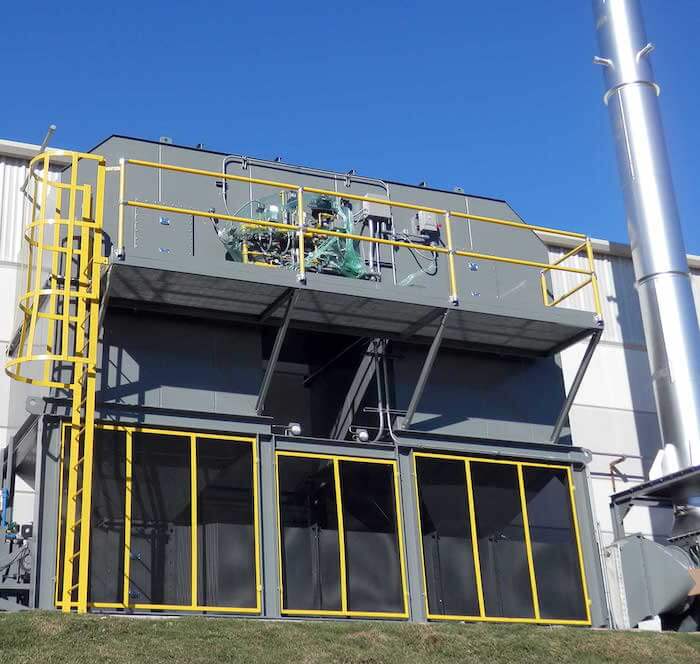
A two-chamber regenerative thermal oxidizer (RTO)
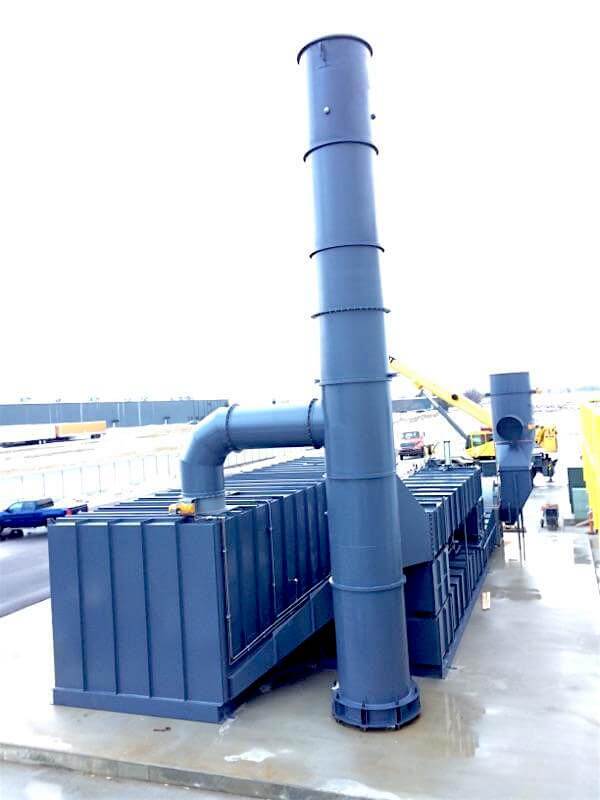
A thermal oxidizer (TO)
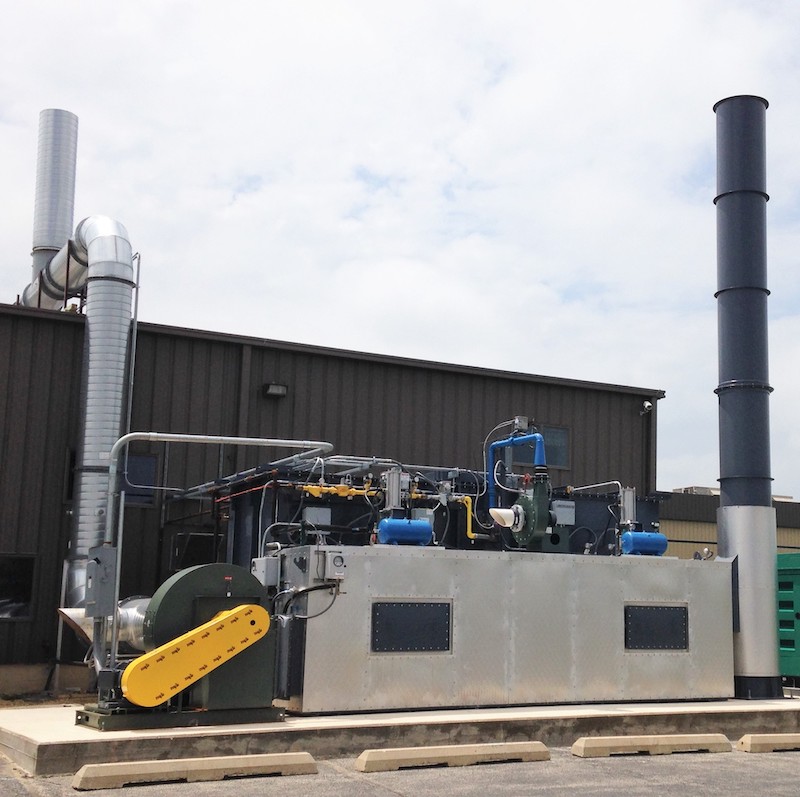
A smaller 10,000 CFM regenerative thermal oxidizer (RTO) on concrete pad.
Thermal Oxidizer Design Calculations
Air Volume Flowrate (CFM)
The volume of process air to be treated is a key consideration. A single thermal oxidizer (TO) system can be designed to handle any amount from 100 CFM (DFTO) to over 80,000 CFM (RTO). Multiple thermal oxidizers can be combined to treat any volume of air.
Each type of thermal oxidizer has a range of air volume flow rates that it can feasibly handle without getting too large or too small (too costly).
Destruction Efficiency of Thermal Oxidizers
Each type of thermal oxidizer can offer a slightly different destruction or removal efficiency. A one-direction flow unit like a direct-fired thermal oxidizer (DFTO) or thermal recuperative oxidizer (TRO) with simple air-to-air heat exchange will offer the highest destruction efficiency of 99%. Most 3-chamber RTOs can also offer 99% DRE. A 2-chamber RTO will be limited to 95-98% DRE due to dirty air that escapes during the periodic switching of air flow direction.
Factors that impact destruction efficiency of thermal oxidizers:
- Temperature
- Residence time
- Air mixing
- Purge cycles (2-can RTOs only)
Retention time, or residence time, is the length of time that a VOC/organic is at the appropriate oxidation temperature. Typically, if a 95% destruction/removal efficiency (DRE) is required, then a residence time of a half a second is adequate. Meaning if the organic is brought up to a temperature of about 1400°F, and maintained at 1400°F for half a second, then 95% of the VOCs will decompose. Both retention time and residence time refer to time inside the thermal oxidizer's combustion chamber. Sufficient air mixing, also known as turbulence, must also be achieved. If the turbulence occurs and if the 1400°F for a half a second is achieved, with adequate oxygen, then 95% of the volatile organics will be destroyed. In some cases, particularly in the chemical industry, oxygen must be added to a process stream. For each organic, a specific temperature and a specific retention time is required to achieve the desired level of destruction. The table above illustrates these points for several VOCs.
Temperatures and Residence Times to Achieve Target Destruction Removal Efficiency (DRE) in Thermal Oxidizers (in °F)
95% DRE | 99% DRE | |||
---|---|---|---|---|
0.5sec | 1.0sec | 0.5sec | 1.0sec | |
Toluene | 1351 | 1317 | 1372 | 1338 |
Benzene | 1489 | 1415 | 1640 | 1640 |
Styrene | 1445 | 1391 | 1480 | 1424 |
How to decide which thermal oxidizer is right for your process?
Key considerations include:
Upfront Cost
Each type of thermal oxidizer has a typical cost that varies based on the size of the equipment. Do you want to: compare rough costs for each type or get a budget cost for your project?Operating cost
Annual operating costs include electricity, natural gas, compressed air (if needed), maintenance costs, and personnel.Break-even point
Evaluate upfront investment cost vs annual operating cost. Different types of thermal oxidizers offer a trade-off between initial cost and operating cost. The lower your upfront cost, the higher your operating cost will be, and vice-versa. Understanding the break-even timing will help you decide which type of thermal oxidizer is the best long-term solution for your company.Energy usage
Energy usage increases with the required airflow and size of equipment, but varies inversely with the upfront investment cost & thermal efficiency of the system. The more expensive your initial cost, the higher your thermal efficiency, and the lower your energy usage, operating costs, and GHG production will be.Destruction efficiency
Regenerative Thermal Oxidizers (RTO) offer only 98% DRE while recuperative thermal oxidizers (TRO) and direct fired thermal oxidizers (DFTO) offer 99%+ DRE.Footprint, Weight, Size
Some types of thermal oxidizers aren't feasible at certain sizes. The size, weight, and footprint of the equipment varies inversely with energy cost.
Thermal Oxidizer Manufacturers
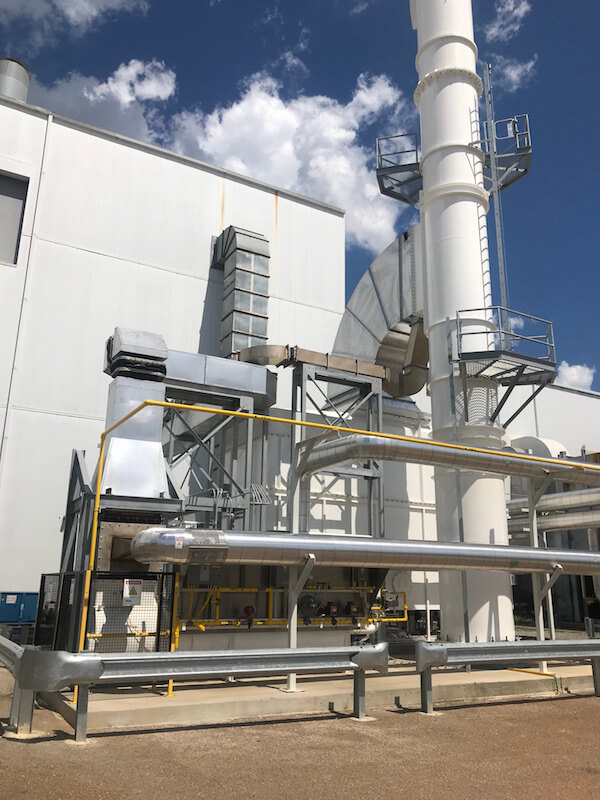
Thermal Oxidizers: Optional Equipment
Ultra Low NOx Emission Burners
Ultra low NOx burners are required by many customers and are legally required in many areas of California as well as several other states. The key to achieving an ultra-low level of NOx is uniform heating and operating at minimum combustion temperature which is achieved by operating lean (lower fuel-to-air ratio). More NOx is produced at higher flame temperatures. NOx emissions do not form in significant amounts until flame temperatures reach 2800°F. Ultra low NOx burners are expensive and typically cost $10,000 - $30,000 USD depending on size.
Flame Arrestor
A flame arrester is a safety device that stops combustion by extinguishing the open flame. The flame arrester can be mounted to the inlet of the oxidizer and utilized to prevent flame propagation in the case the high temp limit or 50% of LEL limit is exceeded, or in the case of a thermal event. Cost is typically in the $10,000 - $15,000 USD range based on size.
Natural Gas Flow Meter
A digital gas flow meter with by-pass look can be installed on the inlet of the gas train. Cost is typically in the $8,000 - $11,000 USD range based on size.
Secondary Heat Exchanger
For sufficiently large thermal oxidizers, the waste heat from the primary heat exchanger (~500°F) may be used to heat process air or liquids. For example, a thermal oxidizer's waste heat can be used to heat drying ovens, generate hot water, heat the plant in the winter, or many other industrial applications.
How Much Should It Cost? Find a Supplier, Get a Quote.
Other Types of Thermal Oxidizers
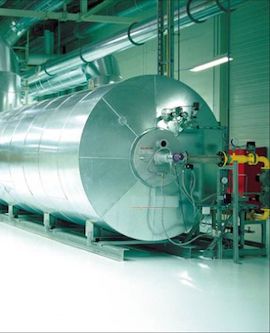
Direct-Fired Thermal Oxidizer (DFTO)
- Gas Flare
- Vapor Combustor
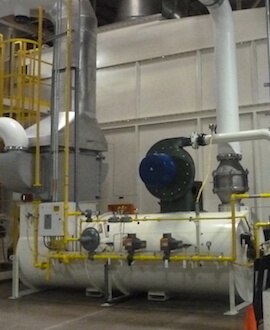
Thermal Recuperative Oxidizer (TRO)
- Thermal Oxidizer with Heat Exchanger (HEX)
Frequently Asked Questions (FAQ)
A new thermal recuperative oxidizer (TRO), meaning a TO with a heat exchanger, will cost more due to the addition of the air-to-air heat exchanger. The smallest recuperative oxidizers cost ~$130,000 USD and the largest will cost over $500,000 USD.
A new regenerative thermal oxidizer (RTO) is even more expensive, due to the extensive ceramic media heat exchange system. The smallest RTOs will cost $250,000 USD and the largest single units cost over $1 million.
- Incoming air volume and temperature (ACFM)
- Desired residence time for VOCs in combustion chamber
- Concentration of VOCs and potential for needing supplemental fresh air to cool the TO
- Type of fan: Should we use a forced draft or induced draft fan? Put another way, should the fan be placed before the TO or after TO? This is determined based on incoming air temperature, the presence of corrosive gases, and the outlet temperature.
- Size of the fan: This is determined based on the air volume (in ACFM) where the fan will be operating.
- Special materials: these are required if the fan will operate in a high-temp or corrosive gas environment
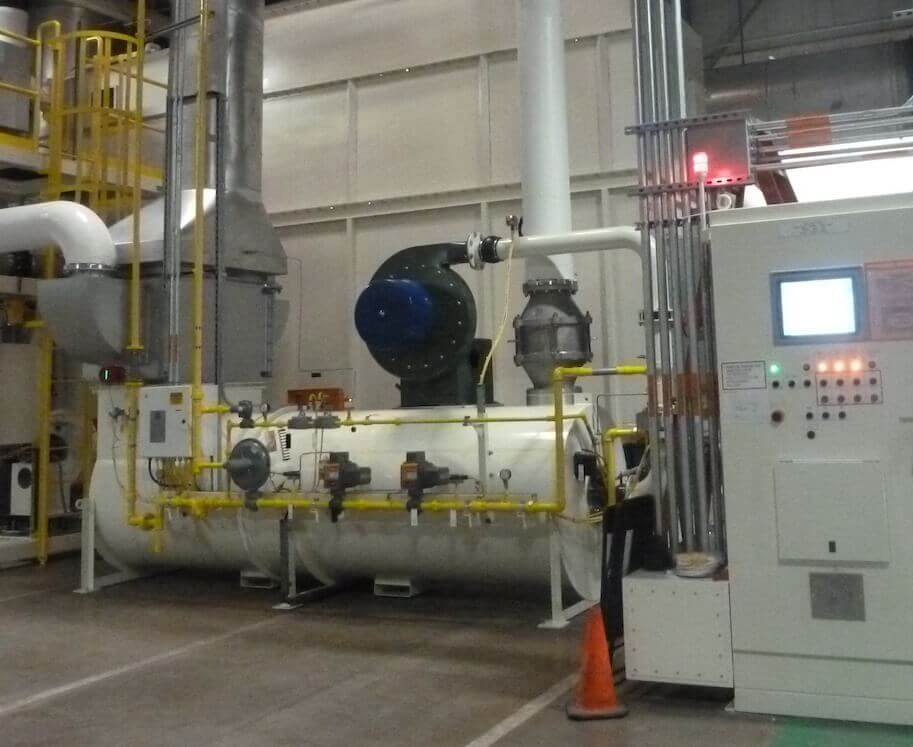
A photo of a thermal recuperative oxidizer (TRO) in an industrial penthouse.